Stainless Steel Condenser Tubes, SS 304/ 316L Condenser Tube, Condenser Tube Supplier & Manufacturer, Condenser Tubes Power Plant
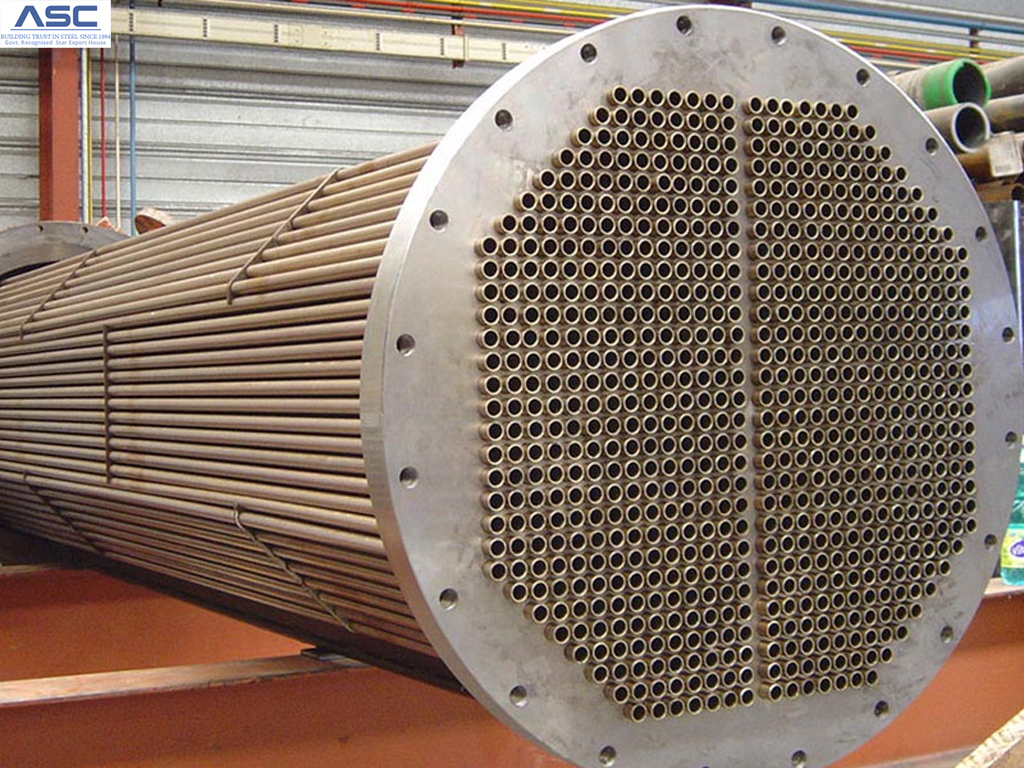
A condenser tube is just a glass cylinder designed for the one and only purpose of quickly
chilling liquids that are kept in a different container. Condenser tubes come in a variety of configurations,
but they all share certain characteristics, including two external glass joints for connecting to other
components, a central glass bulb for heat dissipation, and a small interior glass tube for passing either
water or air through the condenser's centre. Extremely hot liquids and gases can be removed from the heat
source using this procedure, cooled, and then reintroduced back to the storage space where they were
originally stored. A condenser tube not only increases the amount of time that liquids and gases may be used
in machinery, but it also improves the rate at which they operate.
It might be unclear at first why a condenser tube would be required at all. Condenser tubes are largely used
to eliminate waste, which is not as difficult or scientific as some people might believe.
For instance, while boiling water on a stove for cooking purposes, it is simple to maintain the
water level at the proper height within the pot when the cooking apparatus is cool, but as the temperature
rises, some of the water turns to steam and evaporates. The steam would be taken out of the cookware, cooled
back to liquid form, and then added back to the remaining water if a glass cover and a condenser tube were
attached. This example might not seem applicable, but organizations all around the world utilize condenser tubes
because the liquid being heated can be very expensive. Additionally, by controlling the evaporation levels, this
method avoids a lot of the natural waste.
Since glass is the major component of condenser tubes, maintenance is frequently a difficult task that
necessitates frequent inspection and cleaning. When carried out correctly, the condenser tube will have an
increased life span of several years. A proper condenser tube cleaning system would rinse the condenser tubes
when they are not in use to remove any buildup of trace metals or other deposits. On machines that do not deal
with extra solids during the heating process, maintenance is typically performed every three months; on those
that do, it is more regularly.
Condenser tubes are now considerably more prevalent in enterprises due to the cost benefits that result from
their efficient installation. They are particularly common in machinery that works with difficult-to-replace
components. Because of this, you can find them on anything from cheap laboratory equipment to nuclear reactors.
Amardeep Steel Centre is a major producer of high-quality Stainless Steel Condenser Tube. Stainless Steel
Condenser Tube is widely used in heat exchangers, from condensing steam in surface condensers to being part of a
condenser and evaporator refrigeration cycle in a chiller. Stainless Steel Condenser Tubing is often
manufactured with an O.D. of 3/4", 5/8", and 1". SS Condenser tubes can also be improved internally and
externally to improve their efficiency.
Condenser tubes made of stainless steel that are specifically designed for heating, cooling, or reheating fluids
and gases. Precision tubes are frequently found in thermal and nuclear power plants, as well as chemical
processing plants. SS Condenser Tube have a number of standard sizes and grades such as : 304/304L and 316/316L.
304 stainless steel in the most common stainless steel. The steel contains both chromium and nickel metals as
the main non-iron constituents. It is an austenitic stainless steel. It is less electrically and thermally
conductive than carbon steel and isn essentially non magnetic. Type 304 stainless steel is a T 300 series
stainless steel austenitic. It has a minimum of 18% chromium and 8% nickel combined with a maximum of 0.08%
carbon. It is defined as Chromium-Nickel austenitic alloy. Grade 304 is the standard 18/8 stainless that you
will probably see in your pans and cookery tools
Condenser Tubes Specification -
Specification |
|
|
ASTM B622 | C276 (UNS N10276) | Seamless Eddy Current tested |
ASTM B626 | C276 (UNS N10276) and C22 (UNS N06022) |
IA Welded and Annealed - 100% Eddy Current tested IB Welded, Sized and Annealed - 100% Eddy Current tested IIA Welded and Cold Worked - 100% Eddy Current tested IIB Welded and Cold Worked - 100% Eddy Current and Hydrostatically tested |
ASTM A789 | Duplex (UNS S31803) Super Duplex (UNS S32760 and UNS 32750) |
Seamless, Welded, Welded redrawn - 100% Eddy Current tested |
ASTM B516 | Alloy 600 (UNS N06600) |
Welded and Welded redrawn Class 1 - 100% Eddy Current tested Class 2 - 100% Eddy Current and Pressure tested |
ASTM A213 ASTM A269 |
Stainless Steels |
Seamless - 100% Eddy Current tested |
Condenser Tubes Mechanical Properties -
ASTM A213/ ASME SA 213 | Temperature Range (ºC [ºF]) | Yield Stress (min. MPa) | Tensile Stress (min. MPa) | Elongation (min. %) | Hardness (max. Rockwell) |
---|---|---|---|---|---|
TP304H | 590 [1095] | 205 | 515 | 35 | 90 HRB |
TP310H | 590 [1095] | 205 | 515 | 35 | 90 HRB |
TP321H | 600 [1110] | 205 | 515 | 35 | 90 HRB |
TP347/347H | 610 [1130] | 205 | 515 | 35 | 90 HRB |
TP347HFG | 650 [1200] | 205 | 550 | 35 | 90 HRB |
TP316H | 610 [1130] | 205 | 515 | 35 | 90 HRB |
S30432 | 650 [1200] | 235 | 590 | 35 | 95 HRB |
TP310HCbN | 670 [1240] | 295 | 655 | 30 | 100 HRB |
Condenser Tube Chemical Composition
Grades | Carbon | Manganese | Phosphorus | Sulfur | Silicon | Chromium | Nickel | Molybdenum |
---|---|---|---|---|---|---|---|---|
TP304 | 0.08 | 2 | 0.045 | 0.03 | 1 | 18.0-20.0 | 8.0-11.0 | |
TP316 | 0.08 | 2 | 0.045 | 0.03 | 1 | 16.0-18.0 | 11.0-14.0 | 2.0-3.0 |
TP304L | 0.035 | 2 | 0.045 | 0.03 | 1 | 18.0-20.0 | 8.0-13.0 | |
TP316L | 0.035 | 2 | 0.045 | 0.03 | 1 | 16.0-18.0 | 10.0-14.0 | 2.0-3.0 |
Stainless Steel Condenser Tube Sizes & weight Chart
12.70 mm OD | x | 0.6 mm wall | in lengths up to 20 m (65.62 ft) |
15.00 mm OD | x | 1.22 mm wall | in lengths up to 20 m (65.62 ft) |
19.05 mm OD | x | 1.65 mm wall | in lengths up to 20 m (65.62 ft) |
25.40 mm OD | x | 2.11 mm wall | in lengths up to 20 m (65.62 ft) |
38.10 mm OD | x | 2.64 mm wall | in lengths up to 20 m (65.62 ft) |
Stainless Steel Condenser Tube Tolerances
• OD Tolerance: +0.005/-0 in.
• Hardness: Maximum 80 HRB (Rockwell)
• Wall Thickness: ±10%
• Chemistry: Min. 2.5% Molybdenum
Stainless Steel Condenser Tube Pressure Rating
AVE. WALL INCHES | MIN YIELD STRENGTH (PSI) | MIN TENSILE STRENGTH (PSI) | THEORETICAL BURST PRESSURE * (PSI) | WORKING PRESSURE (PSI) 25% OF BURST | THEORETICAL YIELD POINT ** (PSI) | COLLAPSE PRESSURE *** (PSI) | |
---|---|---|---|---|---|---|---|
0.250 | 0.020 | 30,000 | 75,000 | 14,286 | 3,571 | 5,714 | 4,416 |
0.250 | 0.028 | 30,000 | 75,000 | 21,649 | 5,412 | 8,660 | 5,967 |
0.250 | 0.035 | 30,000 | 75,000 | 29,167 | 7,292 | 11,667 | 7,224 |
0.250 | 0.049 | 30,000 | 75,000 | 48,355 | 12,089 | 19,342 | 9,455 |
0.250 | 0.065 | 30,000 | 75,000 | 81,250 | 20,313 | 32,500 | 11,544 |
0.375 | 0.020 | 30,000 | 75,000 | 8,955 | 2,239 | 3,582 | 3,029 |
0.375 | 0.028 | 30,000 | 75,000 | 13,166 | 3,292 | 5,266 | 4,145 |
0.375 | 0.035 | 30,000 | 75,000 | 17,213 | 4,303 | 6,885 | 5,077 |
0.375 | 0.049 | 30,000 | 75,000 | 26,534 | 6,634 | 10,614 | 6,816 |
0.375 | 0.065 | 30,000 | 75,000 | 39,796 | 9,949 | 15,918 | 8,597 |
0.500 | 0.020 | 30,000 | 75,000 | 6,522 | 1,630 | 2,609 | 2,304 |
0.500 | 0.028 | 30,000 | 75,000 | 9,459 | 2,365 | 3,784 | 3,172 |
0.500 | 0.035 | 30,000 | 75,000 | 12,209 | 3,052 | 4,884 | 3,906 |
0.500 | 0.049 | 30,000 | 75,000 | 18,284 | 4,571 | 7,313 | 5,304 |
0.500 | 0.065 | 30,000 | 75,000 | 26,351 | 6,588 | 10,541 | 6,786 |
0.500 | 0.083 | 30,000 | 75,000 | 37,275 | 9,319 | 14,910 | 8,307 |
0.625 | 0.020 | 30,000 | 75,000 | 5,128 | 1,282 | 2,051 | 1,859 |
0.625 | 0.028 | 30,000 | 75,000 | 7,381 | 1,845 | 2,953 | 2,568 |
0.625 | 0.035 | 30,000 | 75,000 | 9,459 | 2,365 | 3,784 | 3,172 |
0.625 | 0.049 | 30,000 | 75,000 | 13,947 | 3,487 | 5,579 | 4,335 |
0.625 | 0.065 | 30,000 | 75,000 | 19,697 | 4,924 | 7,879 | 5,591 |
0.625 | 0.083 | 30,000 | 75,000 | 27,124 | 6,781 | 10,850 | 6,910 |
0.625 | 0.095 | 30,000 | 75,000 | 32,759 | 8,190 | 13,103 | 7,734 |
0.625 | 0.109 | 30,000 | 75,000 | 40,172 | 10,043 | 16,069 | 8,639 |
0.750 | 0.028 | 30,000 | 75,000 | 6,052 | 1,513 | 2,421 | 2,156 |
0.750 | 0.035 | 30,000 | 75,000 | 7,721 | 1,930 | 3,088 | 2,669 |
0.750 | 0.049 | 30,000 | 75,000 | 11,273 | 2,818 | 4,509 | 3,664 |
0.750 | 0.065 | 30,000 | 75,000 | 15,726 | 3,931 | 6,290 | 4,749 |
0.750 | 0.083 | 30,000 | 75,000 | 21,318 | 5,330 | 8,527 | 5,905 |
0.750 | 0.095 | 30,000 | 75,000 | 25,446 | 6,362 | 10,179 | 6,637 |
0.750 | 0.109 | 30,000 | 75,000 | 30,733 | 7,683 | 12,293 | 7,453 |
0.750 | 0.120 | 30,000 | 75,000 | 35,294 | 8,824 | 14,118 | 8,064 |
0.875 | 0.020 | 30,000 | 75,000 | 3,593 | 898 | 1,437 | 1,340 |
0.875 | 0.028 | 30,000 | 75,000 | 5,128 | 1,282 | 2,051 | 1,859 |
0.875 | 0.035 | 30,000 | 75,000 | 6,522 | 1,630 | 2,609 | 2,304 |
0.049 | 30,000 | 75,000 | 9,459 | 2,365 | 3,784 | 3,172 | |
0.875 | 0.065 | 30,000 | 75,000 | 13,087 | 3,272 | 5,235 | 4,126 |
0.875 | 0.083 | 30,000 | 75,000 | 17,560 | 4,390 | 7,024 | 5,152 |
0.875 | 0.095 | 30,000 | 75,000 | 20,803 | 5,201 | 8,321 | 5,807 |
0.875 | 0.109 | 30,000 | 75,000 | 24,886 | 6,221 | 9,954 | 6,543 |
0.875 | 0.120 | 30,000 | 75,000 | 28,346 | 7,087 | 11,339 | 7,100 |
1.000 | 0.028 | 30,000 | 75,000 | 4,449 | 1,112 | 1,780 | 1,633 |
1.000 | 0.035 | 30,000 | 75,000 | 5,645 | 1,411 | 2,258 | 2,027 |
1.000 | 0.049 | 30,000 | 75,000 | 8,149 | 2,037 | 3,259 | 2,796 |
1.000 | 0.065 | 30,000 | 75,000 | 11,207 | 2,802 | 4,483 | 3,647 |
1.000 | 0.083 | 30,000 | 75,000 | 14,928 | 3,732 | 5,971 | 4,567 |
1.000 | 0.095 | 30,000 | 75,000 | 17,593 | 4,398 | 7,037 | 5,159 |
1.000 | 0.109 | 30,000 | 75,000 | 20,908 | 5,227 | 8,363 | 5,827 |
1.000 | 0.120 | 30,000 | 75,000 | 23,684 | 5,921 | 9,474 | 6,336 |
1.000 | 0.134 | 30,000 | 75,000 | 27,459 | 6,865 | 10,984 | 6,963 |
1.250 | 0.035 | 30,000 | 75,000 | 4,449 | 1,112 | 1,780 | 1,633 |
1.250 | 0.049 | 30,000 | 75,000 | 6,380 | 1,595 | 2,552 | 2,260 |
Stainless Tube Steam Condenser Tube Wall Thickness
Gauge | Typical Value in Inch | Thickness Range in Inch |
---|---|---|
19 | 0.042 | 0.038 through 0.042 |
11 | 0.12 | 0.112 through 0.122 |
17 | 0.058 | 0.053 through 0.058 |
15 | 0.072 | 0.066 through 0.074 |
20 | 0.035 | 0.031 through 0.035 |
22 | 0.028 | 0.025 through 0.029 |
10 | 0.134 | 0.126 through 0.136 |
18 | 0.049 | 0.044 through 0.049 |
12 | 0.109 | 0.101 through 0.111 |
9 | 0.148 | 0.140 through 0.150 |
16 | 0.065 | 0.060 through 0.065 |
13 | 0.095 | 0.087 through 0.097 |
14 | 0.083 | 0.075 through 0.085 |
8 | 0.165 | 0.157 through 0.167 |
7 | 0.18 | 0.175 through 0.185 |
Condenser Tube Application & Uses
• Vessels Manufacture
• Chemical Industry
• Potassium Industry
• Sea water desalination
• Refrigeration industry
• Ship building
• Heat recovery
Advantages of Stainless Steel Condenser tube
• Stainless steel Condenser tubes improves system safety and reliability
• Stainless steel seamless Condenser tube have greater corrosion resistance
• Stainless steel Condenser tubes are available in custom lengths
• Stainless steel Condenser tubing reduces the use of fittings, preventing the possibilities of
leaks and other long-term failures
• SS welded Condenser tubes reduced installation costs – installation involves less time and
efforts
Other Types Of Condenser Tubes
SS Condenser 304 Tubes | SS 304L Condenser Tubing |
SS 316 Condenser Tube | SS 316L Condenser Tube |
Seamless Condenser Tubing | SS 201 Condenser Tube |
Stainless Steel Condenser Tube | Stainless Steel Seamless Condenser Tubes |
ASTM A249 Stainless steel condenser tubes | SS Shell and tube condenser |
SS Condenser Capillary Tube | Condenser SS Hollow Section |
Stainless Steel Condenser welded tubing | Stainless Steel Condenser Square Tubing |
SS Condenser boiler tube | SS Condenser Santiary Tube |
SS Condenser Heat Exchanger Tube | SS Condenser Furnace Tube |
SS Condenser Thin Wall tube | SS Condenser Gas Tube Ar 15 supplier |
Stainless Steel Condenser ‘U’ Shaped tubing | SS Condenser Coiled Tubing |
Oval Condenser SS Tube | SS Condenser Rectangle Tube |
We Export Condenser Tube To
Angola, Lebanon, Jordan, Argentina, United Arab Emirates, Iraq, Denmark, Iran, Philippines, Qatar, Kazakhstan, Bolivia, Trinidad & Tobago,Tunisia, Macau, Israel, Afghanistan, Taiwan, Poland, Saudi Arabia, Slovakia, Zimbabwe, Ireland, Bangladesh, Belarus, Spain, Nigeria, Portugal, Singapore, Bahrain, Kenya, China, United Kingdom, Sweden, Algeria, Chile, Nepal, Yemen, Chile, Egypt, India, Pakistan, Netherlands, Namibia, Gambia, Finland, Mexico, Thailand, Ghana, Switzerland, Serbia, Russia, Sri Lanka, Gabon, Czech Republic, Morocco, France, Venezuela, Greece, Japan, Lithuania, Ukraine, Germany, Costa Rica, Iran, Oman, Peru, Tibet, Estonia, Colombia, Australia, Turkey, Bulgaria, Italy, Ecuador, Malaysia, Indonesia, Vietnam, Mexico, Norway, Romania, Libya, South Africa, Hungary, Croatia, Belgium, Poland, Nigeria, Azerbaijan, Puerto Rico, South Korea, New Zealand, Kuwait, Canada, Bhutan, Austria, Mongolia, Hong Kong, United States, Brazil.
We Supply Condenser Tube to
Surat, Cairo, Al Khobar, Caracas, Faridabad, Hanoi, New York, Ernakulam, Kolkata, Pimpri-Chinchwad, Houston, Kuala Lumpur, Pune, Colombo, Melbourne, Aberdeen, Bogota, Jamshedpur, Ankara, Rajkot, Navi Mumbai, Chennai, Calgary, Montreal, Ranchi, New Delhi, Coimbatore, Karachi, Granada, La Victoria, Thane, Perth, Ho Chi Minh City, Rio de Janeiro, Nagpur, Edmonton, Baroda, Haryana, Sharjah, Secunderabad, Santiago, Ludhiana, Muscat, Bhopal, Noida, Thiruvananthapuram, Kanpur, Milan, Los Angeles, Petaling Jaya, Gurgaon, Jakarta, Busan, Abu Dhabi, Hong Kong, Atyrau, Nashik, Bengaluru, Al Jubail, Vadodara, Singapore, Chandigarh, Lagos, Howrah, Hyderabad, Bangkok, Jaipur, Ahmedabad, Toronto, Gimhae-si, Chiyoda, Geoje-si, Riyadh, Sydney, Dallas, Kuwait City, London, Madrid, Istanbul, Ulsan, Indore, Mumbai, Visakhapatnam, Vung Tau, Jeddah, Brisbane, Ahvaz, Dammam, Manama, Port-of-Spain, Algiers, Lahore, Tehran, Seoul, Mexico City, Doha, Dubai, Courbevoie, Moscow.