IBR Pipes and Tubes specification, ibr pipe weight chart, ibr pipe chemical composition, ibr pipe mechanical properties, ibr pipe size chart, ibr pipe manufacturers india, ibr pipe Supplier & Exporter
ASTM 312 / 213, A 53, A106, A333, 335, A 179 / A 210, A/SA 213 IBR Pipes & Tubes Suppliers in India.
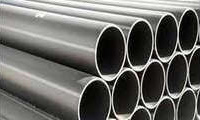
Amardeep Steel is one of the leading suppliers, traders, exporters and reputed stock holders
of IBR Pipe.
IBR (Indian Boiler Regulations) Boiler Pipes and Tubes are specifically designed to meet the Indian boiler
regulations. These regulations set standards for the design, fabrication, inspection, and testing of boilers
and boiler components to ensure safe and efficient operation.
IBR Boiler Pipes and Tubes are made from different materials, such as carbon steel, manganese steels,
molybdenum steel, and chromium-molybdenum steels.. These pipes and tubes are used in a wide range of
applications, including power plants, oil and gas refineries, chemical plants, and other industrial settings.
These pipes and tubes are available in a variety of sizes and thicknesses to meet the specific
requirements of each application. They are also available in various grades such as ASTM A106 Gr B, ASTM A335
P5, P9, P11, P22, and P91, among others.
IBR Boiler Pipes and Tubes undergo rigorous testing to ensure they meet the required standards and regulations.
They are subjected to hydrostatic testing, ultrasonic testing, eddy current testing, and other non-destructive
testing methods to ensure they are free from defects and meet the required specifications.
IBR Boiler Pipes and Tubes are an essential component in any boiler system and play a critical role in ensuring
safe and efficient operation. When choosing IBR Boiler Pipes and Tubes for your application, it is important to
select the right size, grade, and thickness to ensure they can withstand the pressure and temperature conditions
of your system.
IBR Boiler Tube Specification :
Seamless/ Forged/ Bored Pipe | ASTM A335 / A369/ SA369 |
---|---|
Approved Seamless Pipe (OD) | 21.3 - 660mm ( Inch 1/2” – 26”) |
SAW | 16" - 100" NB |
ERW and HFW | 1/2” NB – 24” NB |
LSAW / DSAW | 16’OD TO 54" OD (8 MM TO 50 MM THK) |
Wall Thickness (WT) | 4.5mm to 60mm |
End finish |
BSE -Bevel small end, BOE-Beveled One End, BLE -Bevel large end, BBE -Bevel both ends, PBE -Plain Both Ends, POE -Plain One End, BE -Beveled end, TBE -Treaded Both Ends, TOE -Treaded One End |
Standard Length | 6000mm, SRL, 12000mm, Double Random Length (DRL), 40FT, Single Random Length (SRL), 2000mm, 20FT, Custom Length, 3000mm, DRL |
Schedules | SCH-5, SCH-40, SCH-XS, SCH-5S, SCH-80, SCH-80S, SCH-XXS, SCH160, SCH-STD, SCH-40S, SCH-10S, SCH-10 |
Surface Treatment |
|
Marking by IBR Pipe suppliers |
|
Different methods used by IBR Pipe manufacturers' |
Extrusion, CDW, Cold Drawn Seamless (CDS), Electro Fusion Seam Welded (EFSW), Fabricated, 100% X Ray/ Gamma Ray Welded, Welded, Submerged Arc Welded (SAW), Longitudinally Submerged Arc Welded (LSAW), Seamless, Hot Finish Seamless (HFS), Horizontal Submerged Arc Welded (HSAW), Electric Resistance Welded (ERW) |
Approvals | HAF 604, Merkblatt W0, PED 97/23/EC, Saudi Aramco, NORSOK M-650, AD2000, BP, PED, Shell, EIL, ISO 17025 for Laboratories, KNPC, ONGC, L&T |
Origin of material | Latin-American, Asian, European, UK, Japan, Ukraine, Chinese, Africa, Indian, USA, Japanese, Korean, American, Gulf, Russian |
Certificate | SSC, Sour-Service, EN-10204:3.1, NACE, EN-10204:3.2, HIC |
Equivalent Standards | GOST, API, UNI, BS, SS, ISO, DIN, SAE, JIS, CSA, IS, AISI, GB, ANSI, AWWA, EN, KS, ASTM, NFA |
Test |
Non Destructive Testing , Hardness Test, Hydro test, Hardness, Metallurgical & Stereo Microscopy, Mechanical, Flux Leakage examination or Magnetic Flaw detection, SSC- Sulfide Stress Corrosion Cracking, Creep, Tensile, Macro, Burst Test, Radiography, Charpy V Impact Test, Chemical, Positive Material Identification (PMI), Fine Grain, NACE MR0175, Stress , Ultrasonic Test, Straightness, Ferrite, Eddy current, Micro, Bend TestBend test / Guided Bend, Impact, HIC- Hydrogen-induced Cracking, Surface Roughness Test, TM0177, Charpy V-Notch Test, H2 SERVICE, Ultrasonic, TM0284, IGC- Intergranular Corrosion Test, Salt Spray Test to test Phosphating |
Additional Services and Facility | Cutting, Beveling, Sawing, Laser/ Water Jet Cutting, Tapping, Polishing, Threading |
Material Test Certificate (MTC) provided by IBR Pipe suppliers |
EIL, Ultrasonic Testing (UT), PED, Radiographic Testing (RT), EN 10204 3.1, ISO 9001:2005, ISO 14001:2015, NDE |
Forms and shapes | Oval, Triangle, Round, Rhomboid, Semi-oval, Square, Hollow, Semi-Rhomboid, Rectangle Hollow, Semi-Round, Elliptical |
Coated IBR Pipe suppliers in India | Mild Steel Rubber lining (MSRL), Concrete weight coating (CWC), Black Japan, Coal tar enamel (CTE), Clad Material, Varnish, Black Paint, Galvanizing, Primer, Internal and External Expoxy Coated, Dual Layer ARO Coating, PE Coated, Fusion Bonded Epoxy Coating, Dual Layer FEB, FBE Lining, FBE Coated Pipes, Temporary Corrosion Protection, Anti-Corrosion Paint, LPE Coating And Lining, 3LPP Coated (Three Layer Polyethylene Coating), UV Dual Layer Coating |
Leading IBR Pipe manufacturers/ make | Sumitomo Corporation, Jindal Saw Limited (JSL), Maharshtra Seamless Limited (MSL), Arcelormittal, TATA Steel, Boly Pipe, TMK, Interpipe, Indian Seamless Metal (ISMT), United Seamless Tubulaar Pvt. Ltd (USTPL), JFE, Benteler |
Cutting Techniques | Sawing, Burrless Cuts, Water-Jet, Tapping, Laser |
Chemical Composition of IBR boiler pipes and tubes:
GRADE | Chemical Composition | |||
---|---|---|---|---|
C | Mn | P | S | |
(Max) | (Max) | (Max) | (Max) | |
B | 0.22 | 1.2 | 0.025 | 0.015 |
X42 | 0.22 | 1.3 | 0.025 | 0.015 |
X46 | 0.22 | 1.4 | 0.025 | 0.015 |
X52 | 0.22 | 1.4 | 0.025 | 0.015 |
X56 | 0.22 | 1.4 | 0.025 | 0.015 |
X60 | 0.22 | 1.4 | 0.025 | 0.015 |
X65 | 0.22 | 1.45 | 0.025 | 0.015 |
X70 | 0.22 | 1.65 | 0.025 | 0.015 |
X80 | 0.22 | 1.9 | 0.025 | 0.015 |
Mechanical Properties of IBR Pipe
Mechanical Property | |||||||
---|---|---|---|---|---|---|---|
Tensile | Yield | C. E. IMPACT ENERGY | |||||
Psi x 1000 | Mpa | Psi x 1000 | Mpa | PCM | IIW | J | FT/LB |
60 - 110 | 414 - 758 | 35 - 65 | 241 - 448 | 0.25 | 0.43 | T/L 27/41 | T/L 20/30 |
60 - 110 | 414 - 758 | 42 - 72 | 290 - 496 | 0.25 | 0.43 | T/L 27/41 | T/L 20/30 |
63 - 110 | 434 - 758 | 46 - 76 | 317 - 524 | 0.25 | 0.43 | T/L 27/41 | T/L 20/30 |
66 - 110 | 455 - 758 | 52 - 77 | 359 - 531 | 0.25 | 0.43 | T/L 27/41 | T/L 20/30 |
71 - 110 | 490 - 758 | 56 - 79 | 386 - 544 | 0.25 | 0.43 | T/L 27/41 | T/L 20/30 |
75 - 110 | 517 - 758 | 60 - 82 | 414 - 565 | 0.25 | 0.43 | T/L 27/41 | T/L 20/30 |
77 - 110 | 531 - 758 | 65 - 82 | 448 - 565 | 0.25 | 0.43 | T/L 27/41 | T/L 20/30 |
82 - 110 | 565 - 758 | 70 - 82 | 483 - 565 | 0.25 | 0.43 | T/L 27/41 | T/L 20/30 |
90 - 120 | 621 - 827 | 80 - 102 | 552 - 705 | 0.25 | 0.43 | T/L 27/41 | T/L 20/30 |
IBR Tube Material Grades
Stainless Steel: | TP 304, 304L, 304H, 310, 310S, 316, 316H, 316L, 316Ti, 317, 317L, 321, 321H, 347, 347H, 904L |
---|---|
Carbon Steel: | ASTM A53, ASTM A106 Gr. A , B & C API 5L Gr. A / B, X42 ,X52 ,X60, ASTM A 53 Gr. A/B, ASTM A 333 GR.1/6, ASTM A179, ASTM A192 ASTM A179, DIN 17175/2391 BS 3059/ Gr 1 & Gr 2, ASTM A 334 GR.1/8/6 |
Alloy Steel: | ASTM A335 Gr. P5, P9, P11, P12, P21, P22 & P91, ASTM A213 – T5, T9, T11, T12, T22, T91, ASTM A691 |
IBR Steel Pipe Application
IBR (Indian Boiler Regulations) steel pipes and tubes are used in a variety of applications in the power, energy, and other industrial sectors. Here are some of the common applications of IBR steel pipes and tubes:
- Boiler Manufacturing: IBR steel pipes and tubes are used in the manufacturing of boilers for power plants, industrial processes, and heating applications. These pipes and tubes are capable of withstanding high-pressure and high-temperature conditions.
- Heat Exchangers: IBR steel pipes and tubes are used in the manufacturing of heat exchangers for various industrial applications. These pipes and tubes offer excellent heat transfer properties and are resistant to corrosion.
- Oil and Gas Industry: IBR steel pipes and tubes are used in the oil and gas industry for transporting crude oil, natural gas, and other petroleum products. These pipes and tubes are designed to withstand high-pressure and corrosive environments.
- Chemical Industry: IBR steel pipes and tubes are used in the chemical industry for transporting corrosive chemicals, acids, and other hazardous materials. These pipes and tubes are resistant to corrosion and are capable of withstanding high-temperature and high-pressure conditions.
- Power Generation: IBR steel pipes and tubes are used in power generation applications for transporting steam, hot water, and other fluids. These
pipes and tubes are designed to withstand high-temperature and high-pressure conditions and
offer excellent thermal conductivity properties.
Overall, IBR steel pipes and tubes are highly versatile and can be used in a variety of applications that
require high-performance and durability.
We Supply IBR Pipes & Tubes in listed cities in India
Mumbai, Lucknow, Coimbatore, Imphal, Mysore, Ratlam, Delhi, Kanpur, Darjeeling, Jalandhar, Nagpur, Solapur, Kolkata, Allahabad, Dehradun, Jammu, Nashik, Srinagar, Chennai, Ahmedabad, Faridabad, Jamshedpur, Bhadravati, Chattisgarh, Durgapur, Asansol, Hospet, Bellary, Visakhapatnam, Nellore, Surat, Bangalore, Chandigarh, Ghaziabad, Jhansi, Patna, Siliguri, Hyderabad, Stainless Steel Pipe dealers in Salem, Amritsar, Noida, Kochi (Cochin), Mangalore, Indore, Vadodra, Bhubaneswar, Bikaner, Bhavnagar, Tirupur, Ankleshwar, Warangal, Agartala, Thoothukudi, Stainless Steel Pipe suppliers in Pune, Thiruvanthapuram, Jaipur, Aizawl, Guwahati, Kozhikode, Raipur, Vishakhapatnam, Jabalpur, Bhopal, Gwalior, Ludhiana, Rajahmundry, Thane, Agra, Bhubaneshwar, Gurgaon, Madurai, Rajkot, Varanasi, Bhilai, Haridwar, Meerut, Ranchi, Ahmednagar, Akola, Amravati, Aurangabad, Baramati, Beed, Bhandara, Bhiwandi, Buldhana, Chandrapur, Chimur, Dahanu, Dhule, Dindori, Erandol, Gadchiroli, Hatkanangle, Hingoli, Ichalkaranji, Jalgaon, Jalna, Karad, Khed, Yavatmal, Kolaba, Kolhapur, Kopargaon, Latur, Malegaon, Mumbai, Nagpur, Nanded, Nandurbar, Nashik, Osmanabad, Pandharpur, Parbhani, Rajapur, Ramtek, Ratnagiri, Raver, Sangli, Satara, Shirdi, Shirur, Solapur, Thane, Wardha, Washim, Andhra Pradesh, Jammu and Kashmir, Nagaland, Uttarakhand, Haryana, Lakshadweep, Arunachal Pradesh, Jharkhand, Odisha, West Bengal, Himachal Pradesh, Assam, Karnataka, Punjab, Andaman and Nicobar Islands, Puducherry, Bihar, Kerala, Rajasthan, Chandigarh, Meghalaya, Chhattisgarh, Madhya Pradesh, Sikkim, Dadar and Nagar Haveli, Mizoram, Goa, Maharashtra, Tamil Nadu, Daman and Diu, Tripura, Gujarat, Manipur, Telangana, Delhi, Uttar Pradesh in India.
We Export IBR Pipes & Tubes in listed Country
United States of America, Malaysia, UAE, Indonesia, Saudi Arabia, Iran, Qatar, India, China, United Kingdom, Singapore, Canada, Thailand, South Korea, Turkey, Philippines, Egypt, Germany, Italy, Japan, Russia, Vietnam, Australia, South Africa, Portugal, Morocco, Costa Rica, Kazakhstan, Netherlands, Mexico, Brazil, France, Spain, Taiwan, Nigeria, Bangladesh, Kuwait, Iraq, Ukraine, Poland, Jordan, Romania, Oman, Hong Kong, Venezuela, Colombia, Norway, Chile, Trinidad & Tobago, Greece, Czechia, Belgium, Sri Lanka, Cyprus, Angola, Myanmar (Burma), United Kingdom, Canada, South Korea, Thailand, Netherlands, Spain, Turkey, Australia, Mexico, Pakistan, Vietnam, Brazil, Philippines, France, Taiwan, Poland, South Africa, Russia, Nigeria, Kuwait, Czechia, Norway, Romania, Egypt, Oman, Sweden, Belgium, Hong Kong, Israel, Colombia, Switzerland, Denmark, Finland, Argentina, Venezuela, Peru, Ukraine, Chile, Bangladesh, Portugal, Ireland, Austria, Algeria, Greece, Iraq, New Zealand, Slovakia, Hungary, Kazakhstan, Slovenia, Lithuania, Serbia, Sri Lanka, Bahrain, Bulgaria, Morocco, Tunisia, Croatia, Jordan, Ecuador, Trinidad & Tobago, Estonia, Azerbaijan, Ghana, Lebanon, Cyprus, Dominican Republic, Latvia, Libya, Costa Rica, Cambodia, Macedonia (FYROM), Belarus, Jamaica, Palestine, Turkmenistan